Tech Success: Avexus tightens Air Force maintenance
As the world's largest facility for overhauling airplane landing gear, the Air Force's Ogden Air Logistics Center in Utah works on the wheels, brakes and assemblies of some of the world's most complex aircraft.
As the world's largest facility for overhauling airplane landing gear, the Air Force's Ogden Air Logistics Center in Utah works on the wheels, brakes and assemblies of some of the world's most complex aircraft.And because the Air Force wants to keep its F-16 fighters, B-1 bombers and C-5 cargo aircraft ready to fly, the center is constantly seeking to shave time off maintenance and overhauls.This is why the center purchased the maintenance, repair and overhaul, or MRO, software from Avexus Inc., San Diego, said Dee Mackliet, production control chief for the landing gear division at Ogden.The software was installed as part of a project to tighten maintenance schedules through commercial best practices. It helped the center improve its on-time delivery rate from 15 percent to 70 percent, and generated an 89 percent increase in accuracy of accounting for work in progress, according to an Avexus case study of the operation.Ogden "didn't have any real capability to track items when they were in a shop, or [track] what state of repair they were in. And they didn't have due dates assigned for those end items," said Mike Schooler, Dynamics Research Corp.'s program manager for the implementation project. DRC of Andover, Mass., provides engineering, technical and logistics support to the Air Force base.When other aircraft repair facilities would send landing gear components to Ogden for an overhaul, they would not get a definite date telling them when the overhauled assemblies would be returned."This software helped them to change that culture," Schooler said.The implementation was the result of an assessment that DRC made of the center's polices and procedures. It recommended using enterprise resource planning software to replace the eight standalone systems then in place.The Air Force itself had installed a unified system to better track work schedules before, but the results were unsatisfactory, Mackliet said."It tried to rope together all the stovepiped systems. That didn't work too well. You have a lot of timing issues when you don't share a common database," he said.Over a period of a year, an evaluation team comprised of integrator and center personnel narrowed an initial list of possible ERP providers down to three: Western Data Systems (recently acquired by Manugistics Group Inc., Rockville, Md.); Cincom Systems Inc., Cincinnati; and Avexus, according to Schooler.Avexus' Impresa software, built on an Oracle Corp. platform, was chosen because it was tailored to MRO work, Schooler said."It has total ERP functionality for inventory control, shop-floor control and materials requirement planning and all those things ERP systems do. And it ties all that functionality together in an integrated package geared toward MRO shops," he said.A pilot project began in the strut repair shop in fall 2000, and a full rollout of 210 seats was in place by March 2001.For the Air Force, the software provides more exact estimates of when landing gear will be ready for use. Before, the center could only estimate how many assemblies it could turn over in a quarter. Now it can pinpoint those estimates down to weeks and even days.The system also helps the Ogden center pinpoint the trouble spots in the repair process that slowed turnaround times."We finally have visibility," Mackliet said. "We've never been able to break down problems we've been having before. Now, we've found several problems that we've addressed."The center, for example, can compare orders against inventory to forecast when it will run short of parts that require long lead times to acquire. "We've uncovered shortages, and because of this we were able to get shipments out that I know we wouldn't have gotten out otherwise," he said.The software also aligns bills of materials that list each part in an assembly against the in-house stock of replacements. If a part needs to be replaced, the mechanic doesn't need to track it down manually. Considering that the landing gear for a C-5 aircraft has 63 spreadsheet pages of parts that must be checked, the automated system dramatically streamlines the process, Mackliet said.Although Avexus would not reveal the cost of the Ogden deal, Michael Grad, vice president of sales, said software licensing is based on a "per-seat," concurrent, user-based pricing model, with the maintenance and support contract as part of the agreement.Avexus can subcontract for integrators who implement the software in specific projects and want assistance in implementation, as was the case at Ogden. Or the integrator can set up an internal practice to offer the solution independently, Grad said.The system has been used to handle repairs of complex equipment by defense and aerospace companies, such as BAE Systems Plc., Farnborough, U.K.; TRW Inc., Cleveland; and the Boeing Co., Chicago."Our software can be part of a larger solution," Grad said. "It's not uncommon in the federal sector for a systems integrator to use our software with other solutions in the enterprise."The software also is used by Pemco Aeroplex Inc., Birmingham, Ala., which runs a facility for maintaining, repairing and overhauling Air Force aircraft. Taking advantage of the software's Web-enablement, the Naval Aviation Pacific Repair Facility uses Impresa to assess aircraft on carriers at sea so that repairs can be made more quickly when they return to shore.One advantage Avexus can offer integrators is that the software is already compliant with a number of federal and industry standards, said Tom Zlockie, director of sales for the federal systems division of Avexus.The software can interface easily with the Military Standard Requisitioning and Issue Procedures, or Milstrip as well as software using the standards for federal logistics data, also known as Fedlog. It interfaces with the Air Transport Association's SPEC2000, a standard for trading aircraft logistics information.Michael Burkett, an analyst with research company AMR Research Inc., Boston, praised the company's software for user interface and its flexibility to accommodate unique work orders and track costs.The Ogden team praised its ease of use. "We found that the Avexus product was easy to work with and easy to implement, compared to other commercial products that members of the team have worked with before," Schooler said. XXXSPLITXXX- Implement enterprise-level tracking of maintenance, repair and overhaul of aircraft landing gear Agency: Air Force. Ogden Air Logistics Center, Utah Dynamics Research Corp., Andover, Mass. Avexus Inc., San Diego Improve reporting on the status of aircraft landing assemblies being overhauled so aircraft downtime is shortened. Incompatible inventory and scheduling systems could not present a complete picture of repair process. Avexus Inc.'s Impresa ERP software, which is tailored for tracking repair work of complex aircraft assemblies. With an automated system that track parts and repairs from start to finish, the Ogden center improved its on-time delivery of overhauled aircraft from 15 percent to 70 percent.
Parts and repair tracking software helps keep aircraft flying
If you have an innovative solution that you recently installed in a government agency, contact Staff Writer Joab Jackson at jjackson@postnewsweektech.com.
Project:
Integrator:
Partner:
Goal:
Obstacle:
Solution:
Payoff:
If you have an innovative solution that you recently installed in a government agency, contact Staff Writer Joab Jackson at jjackson@postnewsweektech.com.
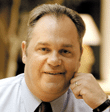
Tom Zlockie, director of sales for the federal systems division of Avexus.
Washington Technology photo by Olivier Douliery
Integrator:
Partner:
Goal:
Obstacle:
Solution:
Payoff:
NEXT STORY: High-flying solution